製品ライフサイクルの短縮化や新技術ニーズの高まりといった市場の変化に対応できるシステム開発や製品開発の手法として、MBDやCAEが注目されています。
今回の記事では、MBDとCAEの違いとともに、MBDやCAE導入に際して発生するメリットやデメリット、デメリットへの対策方法を解説します。
テクノプロ・デザイン社ならシステムやツールの選定、MBDの構築といった面での支援はもちろん、人材育成やコンサルティングも可能です。モノづくりからIT産業まで幅広いテクノロジーに秀でたエンジニアを7000人以上有し、日本全国に展開している拠点から、確実なソリューションを迅速に提供します。お気軽にご相談ください。
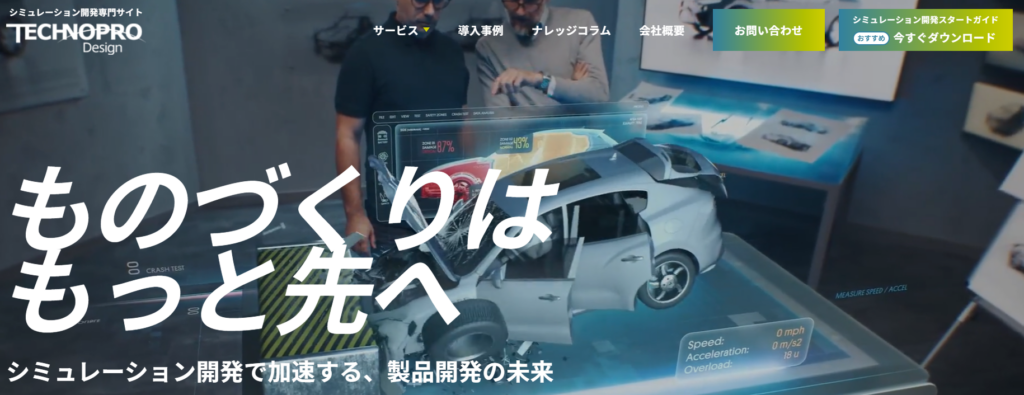
MBDとCAEの概要と違い
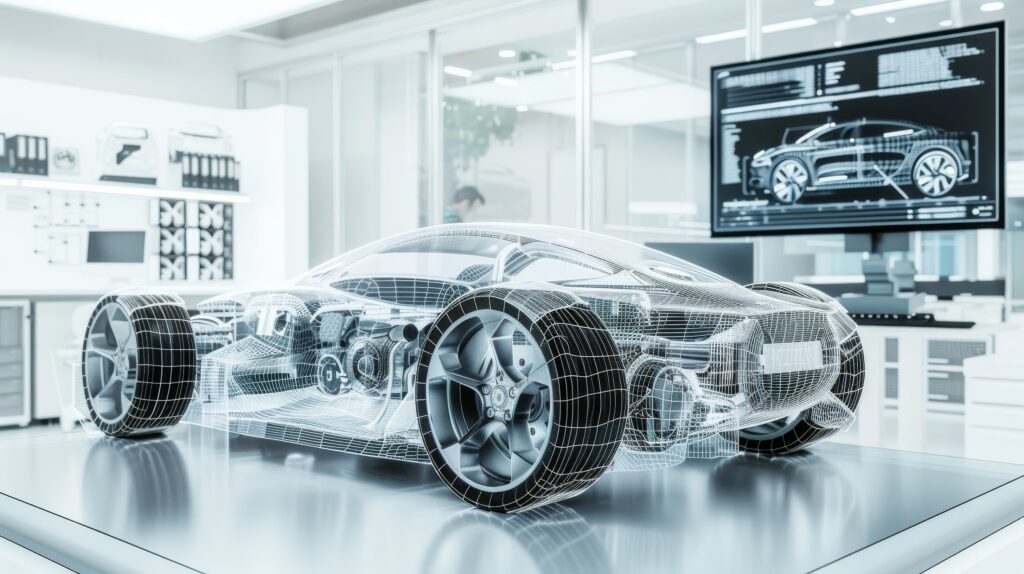
MBDとCAEは、業務効率化、安全性の担保と工程の短縮の両立、コスト削減などを目的に導入される開発手法です。MBD・CAEの概要と、両者の違いを解説します。
MBDとは
MBDとは「Model Based Development」の略語で、モデベース開発とも呼ばれています。制御システムの設計段階で、制御システムの仕様をモデルで表現し、モデルをPC上でシミュレーションさせて動作検証を行いながら仕様の精度を高める開発手法です。
モデルは数式などを用いて制御システムを構成する一部の機能を表現し、入力に対して出力を行うものです。これらのモデルを組み合わせて制御モデルと制御対象モデル(プラントモデル)を作成し、制御システムを模擬します。開発を通じてモデルを活用することで、制御システム開発の効率化や工程の短縮化、コストの削減などが実現できます。
MBD(モデルベース開発)についての詳しい解説は以下の記事を参考にして下さい。
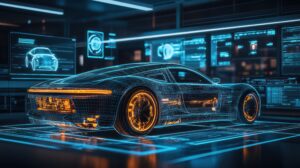
CAEとは
CAEとは「Computer Aided Engineering」の略語です。コンピュータ上で製品に対する物理現象をシミュレーションすることで、製品の設計や分析を支援する仕組み、または支援を実現するツールを指します。
CAEには多くの解析方法が存在します。代表的なものを以下の表にまとめました。
解析方法 | 特徴 | 派生する解析方法 |
構造解析 | 製品へ機械的負荷をかけた、または一定の環境条件下での挙動を検証、評価する解析方法 | ・応力解析…構造物に力をかけたときの物体内部に生じる力(応力)や変形を調べ、一定の条件下で製品が破損に耐えられるかを検証する。つり合い状態を解く構造解析の静解析にあたる ・振動解析…構造物の共振周波数および共振時の変形や,振動を印加した時の応答を検証する。運動方程式を解く構造解析の動解析に分類される。評価される項目に応じて固有値解析,時刻歴応答解析,周波数応答解析等がある。 |
熱解析 | 製品の熱に関する現象をシミュレーションし、評価する解析方法 | ・熱伝導解析…構造物内部の熱エネルギーの移動現象を解析し,構造物内の温度分布を分析する方法。 |
流体解析 | 気体や液体の流れをシミュレーションすることで、流れや温度の分布などを分析する解析方法 | |
電磁界解析 | 電気機器や回路の電磁界を解析、評価を行う解析方法 |
ほかにも、音響解析・鍛造解析・鋳造解析・樹脂流動解析などシミュレーションの対象となる加工方法や物理現象に応じ様々な解析手法があります。また,複数の物理領域を連成させる,熱応力解析や熱流体解析もあります。
CAEはコンピュータ上で物理現象を再現(シミュレート)することで実機による検証作業(試作)を大幅に削減することができ、設計品質の向上,開発コスト削減が実現できます。
MBDとCAEの違い
MBDは設計から検証、実装に至るまで制御システムの開発を通じてモデルを活用し、シミュレーションで動作検証を行う開発手法です。
一方でCAEは物理的または科学的な変化や環境条件下のシミュレーションを、実機不要で検証できる手法を指します。
CAEが各シミュレーションの解析方法や技術そのものを指しているのに対して、MBDはモデルをベースとした開発手法を指します。
MBDとCAEのメリット
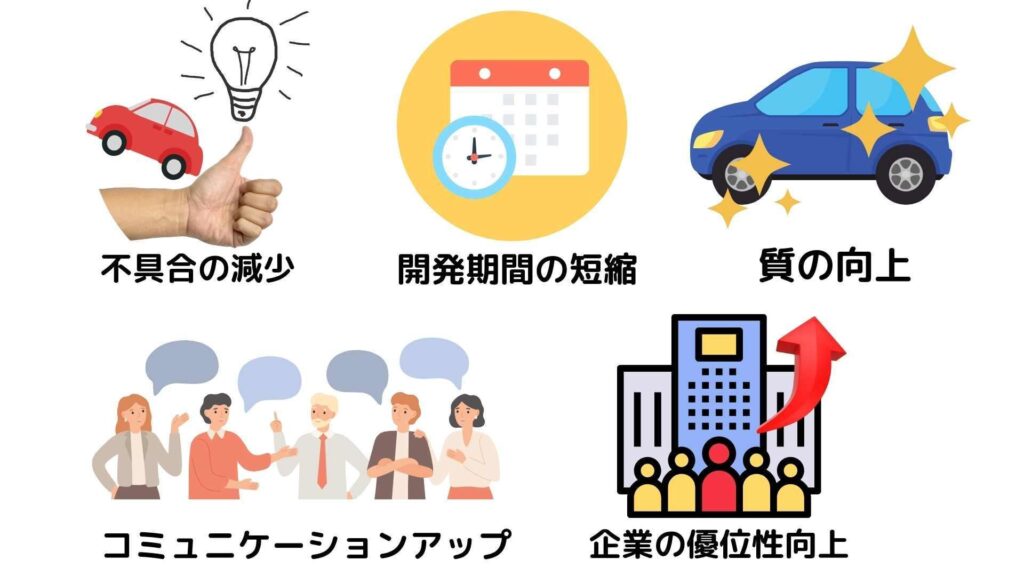
MBDとCAEは製造業のシステム開発および検証に多くのメリットが得られます。経済産業省中国経済産業局の「MBD/CAE 等の導入・活用の手引き・事例集」によれば、「MBDまたはCAEを導入・活用による具体的な効果・メリット」についてアンケートまたはヒアリングを行ったところ、「不具合の減少」が80%、「開発期間の短期化」が64%、「製品(サービス)の質の向上」が60%という結果が出ました。
調査結果を元に、MBDとCAEがもたらすメリットを解説します。
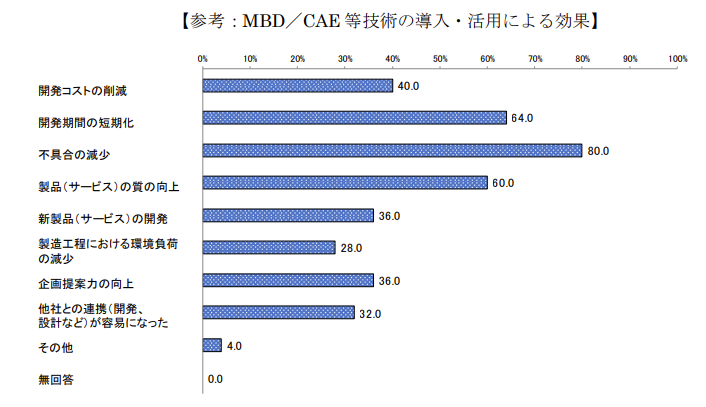
不具合の減少
MBDやCAEは実機不要でシミュレーションによる検証ができるため、実機での検証を行う前の段階から高い精度での設計が可能です。シミュレーションで十分な検証を行うことで、実機での試作の回数は大幅に削減できます。
新規製品の設計は従来の組込み開発およびCAE未実装の場合、類似製品の仕様を流用する、経験に基づいて設計を進める、試作実機による検証実験を繰り返して設計を明確にする、といった不明瞭な要素が入り込んだり、実機による試作を繰り返すことでの負担増などの問題点がありました。
一方、MBDとCAEによるシミュレーションを行うことで、コスト面、スピード面でも検証の負担が減り、検証の精度も増します。シミュレーションの解析結果を元に、不備が予測される部分が把握できることも精度向上につながります。
開発期間の短縮化
MBDやCAEによる検証や解析を活用することで、初期段階からの不具合や設計ミスを把握できる、または高精度での設計が実現するため手戻りが防げます。手戻りが減るので発期間の短縮化にもつながるでしょう。
実機不要で検証ができるため、実機の完成を待たずにシミュレーションができるのも開発期間の短縮をもたらします。ヒアリング対象の企業からは、試作の実験にかかる時間を約40%削減することができた、残業をする社員が少なくなったという事例も出ています。
MBD開発工程の全体ではな検証段階だけHILSを導入する、またはCAEを導入する方法もあります。
また、ヒアリング対象の企業にはHILSやCAE導入を内製化せず、外部の支援サービスを利用して構築した事例もありました。
たとえばヒアリング対象の企業の中には解析を外注し、その分の時間を別の業務に充てることで、効率的に作業を進めている企業や、合弁会社に解析を委託することで、外注と技術的なノウハウ蓄積の両方を実現している企業の事例もあります。
製品(サービス)の質の向上
不具合の減少や開発期間の短縮化によって、製品(サービス)の質の向上にもつながります。
たとえば不具合の減少によって自動車等の強度設計が向上した事例もありました。自動車製造における強度設計は安全のための重要事項です。MBDやCAEを用いた設計によって不具合の発生を防止でき、製品(サービス)の質の向上にもつながります。
MBDやCAEは、現実での実験が困難なシミュレーション環境での検証や解析も可能です。たとえば製品に非常に強い負荷をかける、大量の検証を試行する、故障や不具合を前提とした検証を行うことで、製品の品質や安全性の向上にも有効です。
社内のコミュニケーションの活性化
従来の実機による検証よりも、MBDやCAEのモデルやPC上でのシミュレーションは検証に関する負担が少ないことから、気軽に実施できる傾向があります。検証が気軽に実行できることで、検証結果や分析に対する意見を言いやすい雰囲気も醸成されるでしょう。製品に対するさまざまなアイディアが出るようになったという企業も多いです。
また解析結果を映像・画像で見られるため、結果をイメージしやすくなります。解析や検証に関する理解が深まることで、メンバー間のコミュニケーションの活性化につながります。
企業の提案力や優位性の向上
解析結果を直感的に把握できるようになったことで、顧客に対しても自社製品の信頼性、安全性を分かりやすく提示できます。現実では不可能な検証も含めて繰り返しシミュレーションを行えば、自社製品が強い負荷に耐えられる設計であることなどの証明にもなるでしょう。
MBDやCAEは自動車分野を中心にメーカー各社の推進が浸透しているため、MBDやCAEをすでに導入している企業として優位性を保つことにもつながります。
【関連記事】以下の記事ではモデルベース開発のメリットについて詳しく解説しています。
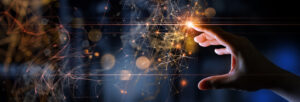
MBDとCAEのデメリットと対策方法
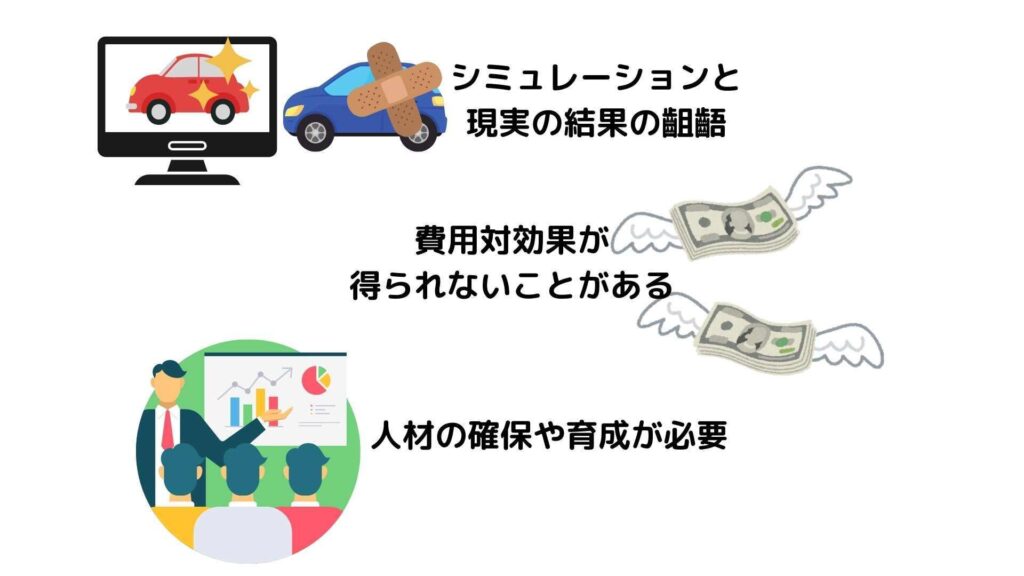
経済産業省中国経済産業局の「MBD/CAE 等の導入・活用の手引き・事例集」で提示されているMBDとCAEの課題を参考に、MBDとCAEのデメリットとその対策方法を解説します。
シミュレーションと現実の結果の齟齬
シミュレーションと現実の結果に齟齬が生じる場合があります。おもな原因はデータ不足とソフトウェアの機能不足です。
現実の結果とシミュレーションとの照合データに不足がある場合は、検証を繰り返し、データを蓄積し、徐々にシミュレーションの精度を高めていく必要があります。そのためには解析だけでなく、解析結果の照合も作業工程に組み込んでシステム化することが重要です。
ヒアリングした企業のなかには、シミュレーションと現実との照合結果の相関をマニュアル化してまとめ、自社における解析の標準化を図り、製品の品質向上を達成した事例もありました。
自社の目的や解決したい課題に適合した機能がソフトウェアやツールに搭載されていない場合は、ソフトウェアやツールをアップグレードするか、サポート体制が整っているベンダーを選ぶ、ソフトウェアやツール選定を外部サービスに依頼する、といった方法があります。
特に自社製品が独自の環境や仕様を有している場合は、汎用的なソフトウェアやツールでは対応できないことがあります。自社の製品に適合したソフトウェアやツールを選びましょう。
費用対効果が得られない
MBDやCED導入時、ソフトウェアやツールの導入をはじめとした初期費用が発生します。導入後効果が得られない、現場に定着しないなどの理由で費用対効果が得られないことがあります。あらかじめ、どの程度の予算が必要か試算しておきましょう。
費用対効果の試算はまずシミュレーションの導入によって、各製品の製造工程で削減できる費用を予測します。次に「製品の数×削減できるコスト」の計算で、おおまかに算出できるでしょう。
ソフトウェアやツールの購入だけでなく、それらを現場に定着させる環境構築のための費用も算出しておきましょう。
人材の確保や育成が必要
MBDやCAEを導入するには、コーディングやプログラミングといった知識といった専門的な知識やスキルを持った人材が必要です。専門的な知識やスキルを持った人材を採用する、または社内でマニュアルやOJTによって育成する仕組みを構築する必要があります。
ヒアリング対象企業の中には、工業高校などで学び専門的な技術やスキルをもった人材を採用する事例がありました。自社にMBDやCAEに関する知見がない場合に、外部支援サービスのコンサルティングなどを利用し、少しずつノウハウを蓄積していった事例もあります。
また、ツールやソフトウェアの操作方法や、シミュレーションの解析を正確に行うための現場の知見も必要です。適切な解析や評価、設計へのフィードバックを行うには、シミュレーション結果だけでなく、現実での結果を比較する力が求められます。MBDやCAEの担当者と現場が連携できる仕組みを構築するなどの工夫を設けましょう。
まとめ
MBDとCAEの概要や違い、メリット、デメリットとその対処法を解説しました。MBDやCAEは自動車分野をはじめ製造業で推進されている技術です。自社に人材やノウハウがなく、構築が難しい場合には外部の支援サービスを利用し、MBDやCAEを構築した企業も多くあります。
また、テクノプロ・デザイン社では多角的なモデルベース開発支援サービスを提供しています。要件定義からモデリングまでのシームレスな設計をはじめ、モデルベースシステムズエンジニアリングの構築支援、モデルベース開発やCAE環境構築に関する人材育成やコンサルティング支援も可能です。お客様の課題に合わせたモデルベース開発支援をご提案いたしますので、ぜひお気軽にお問合せ・ご相談下さい。
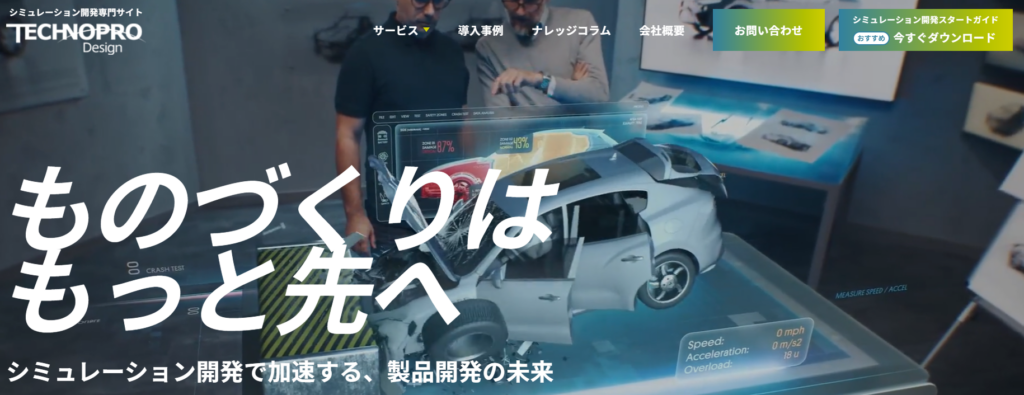